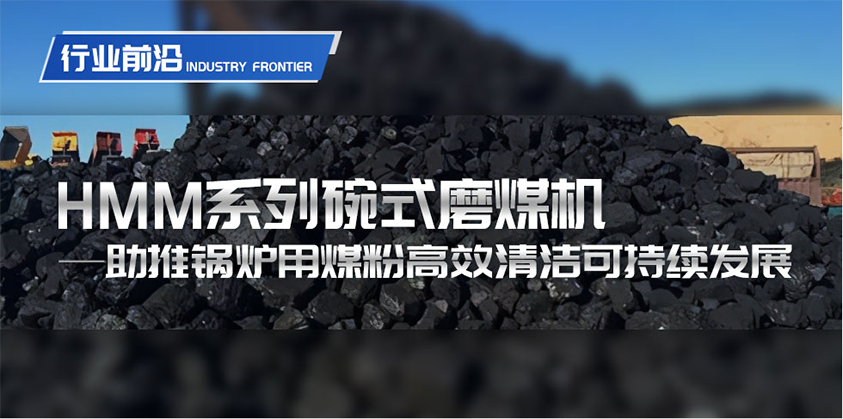
As a traditional energy source for the country, coal's core position cannot be shaken in the short term. Under the trend of environmental protection and emission reduction, the promotion and utilization of clean coal powder is one of the important means to promote energy transformation. Guilin Hongcheng HMM bowl mill, with significant advantages such as high efficiency, environmental protection, and intelligence, will assist in the production of boiler coal powder and promote the green, intelligent, and sustainable development of the energy industry.
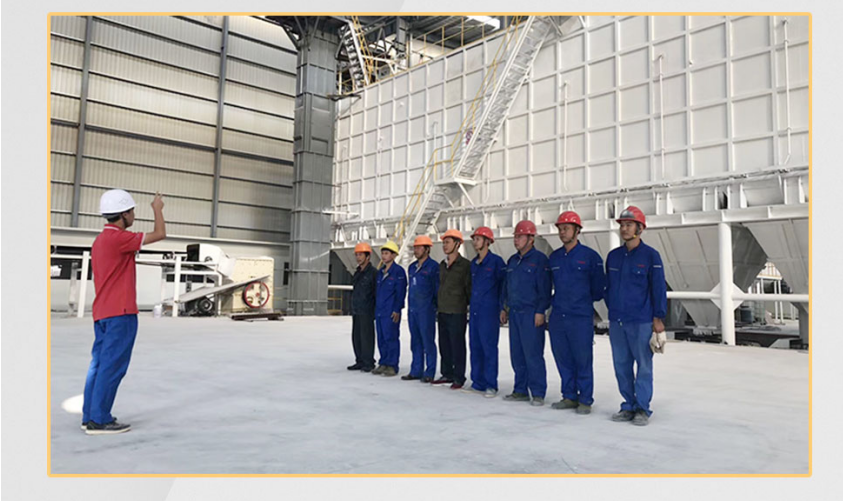
1.Classification of coal powder for boilers
1)Power plant boiler: Power plant boilers are mainly used for electricity production in power plants, providing power equipment for converting chemical energy into steam heat energy for a large amount of fuel. It has a wide adaptability to coal types, but requires moderate heat value and appropriate volatile matter in the furnace, while reducing the content of impurities such as sulfur and ash. The calorific value is generally between 5500-7500 kcal/kg.
2)Industrial boilers: Industrial boilers are mainly used for steam supply in the production of food, textile, chemical, pharmaceutical and other enterprises, and can also be used for urban heating. Usually, low ash, low sulfur, low phosphorus, high volatile matter, and high calorific value raw coal or washed coal are selected as raw materials, and a certain proportion of desulfurizers and flame retardants are added.
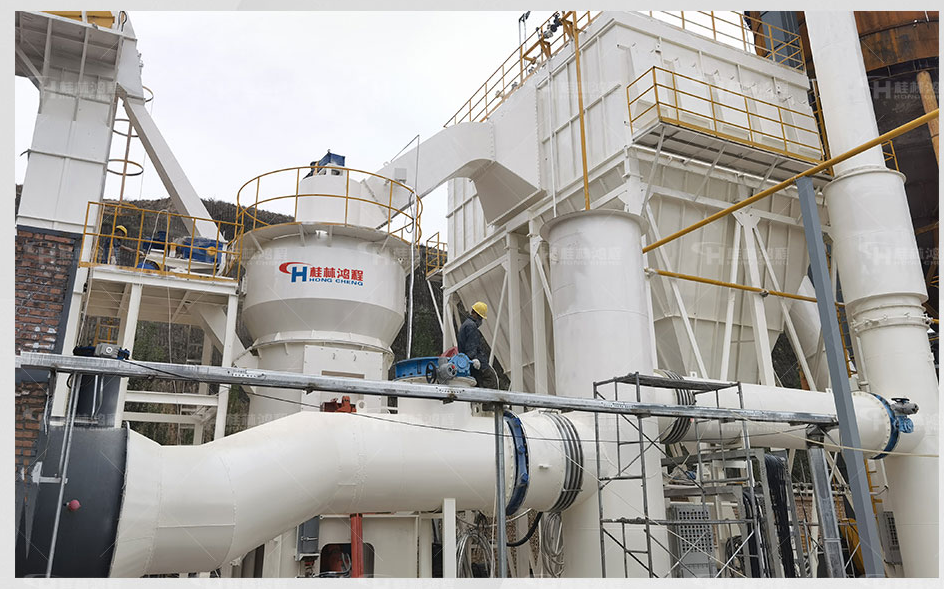
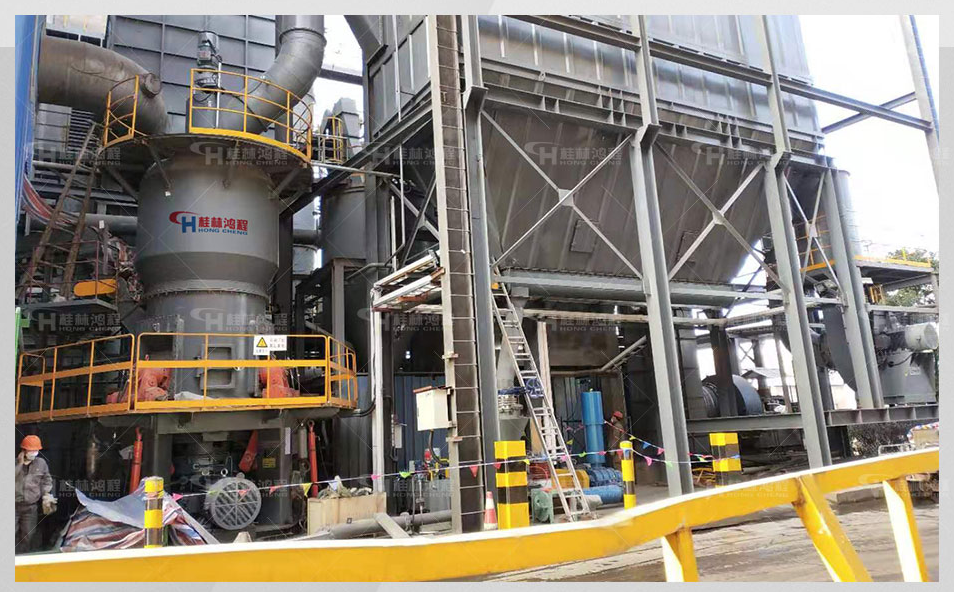
2. Steps for using coal powder for boilers
1)Coal powder preparation: Select suitable coal as raw material based on the combustion requirements and coal quality characteristics of the boiler; The raw coal is crushed into small pieces by a crusher and then sent to a coal mill for grinding to prepare coal powder that meets the requirements of boiler combustion.
2)Coal powder conveying: The prepared coal powder is conveyed to the coal powder silo near the boiler through a pneumatic conveying system (such as air conveying or nitrogen conveying), and then fed into the coal powder burner in a quantitative and uniform manner through a coal feeder or other coal feeding equipment according to the combustion requirements of the boiler.
3)Coal powder injection: Coal powder is mixed with air (primary and secondary air) in a coal powder burner, preheated and ignited before being injected into the boiler furnace. During the injection process, the pulverized coal particles ignite and burn rapidly at high temperature, releasing a large amount of heat energy.
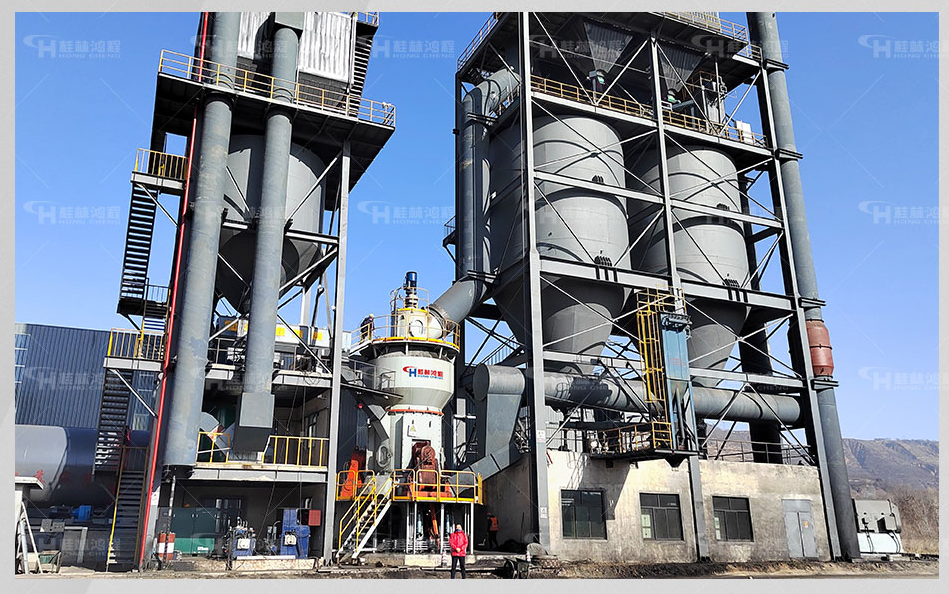
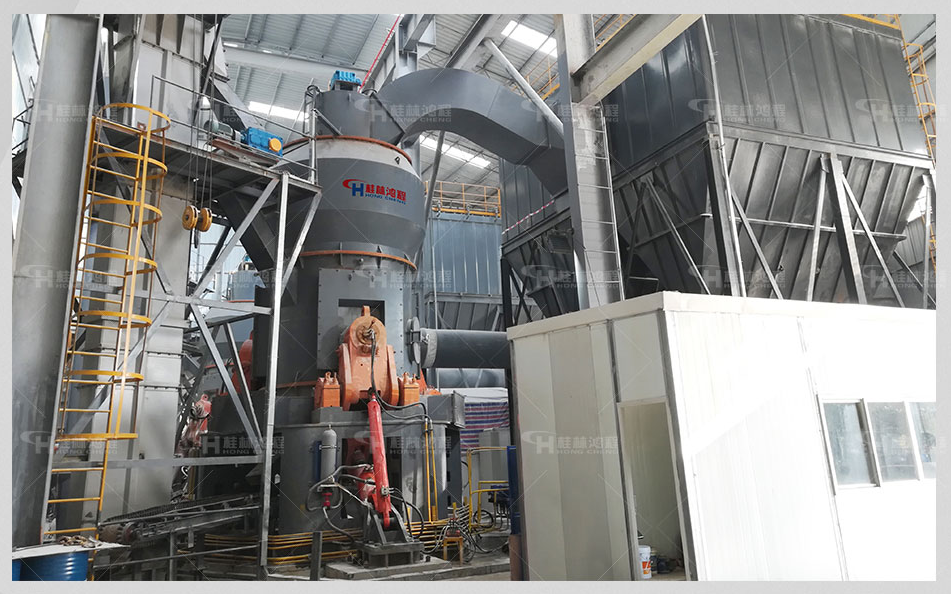
3. Advantages of using coal powder for boilers
1)Improving combustion efficiency: After grinding, the particle size of coal powder decreases, and the surface area increases and becomes uniform, which is conducive to chemical reactions during combustion and allows coal powder to come into contact with oxygen more fully, thereby improving combustion efficiency. At the same time, the combustion speed is fast, the burnout rate is high, and the thermal efficiency is also improved.
2)Helps with energy conservation and emission reduction: Due to the high combustion efficiency of coal powder, the same quality of coal powder can release more heat energy, thereby reducing energy consumption. In addition, the emissions of pollutants such as sulfur dioxide, nitrogen oxides, and particulate matter generated by coal powder combustion are relatively low, which helps to reduce environmental pollution.
3)Improving operational stability: The flame formed during coal powder combustion is stable and evenly burned, which helps to enhance the operational stability of the boiler. Meanwhile, modern industrial boilers often adopt automated control systems, which can accurately control parameters such as coal powder feeding rate and air volume, ensuring that the boiler operates under optimal conditions.
4)Significant economic benefits: Coal fired boilers have significant energy-saving effects compared to traditional boilers, which can save a large amount of coal and reduce production costs. In addition, the coal powder boiler adopts advanced combustion technology and control system, which can achieve efficient and stable operation of the boiler, thereby reducing fuel waste and downtime.
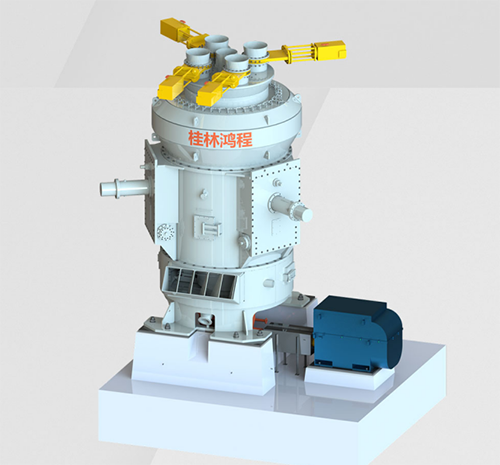
4. HMM series bowl coal mill
The HMM series bowl mill is a high-efficiency, low consumption, adaptable, energy-saving and environmentally friendly coal grinding equipment developed by Guilin Hongcheng based on the market demand and coal powder characteristics of power coal. It is specifically designed for grinding, drying and sorting coal directly blown from boilers, and is an ideal choice for coal powder preparation in power plant boilers and industrial boilers.
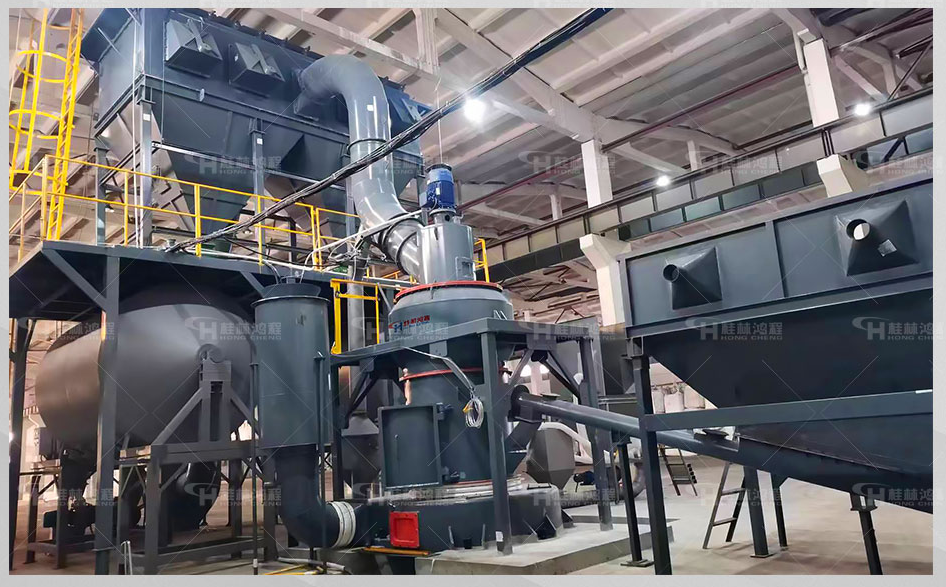
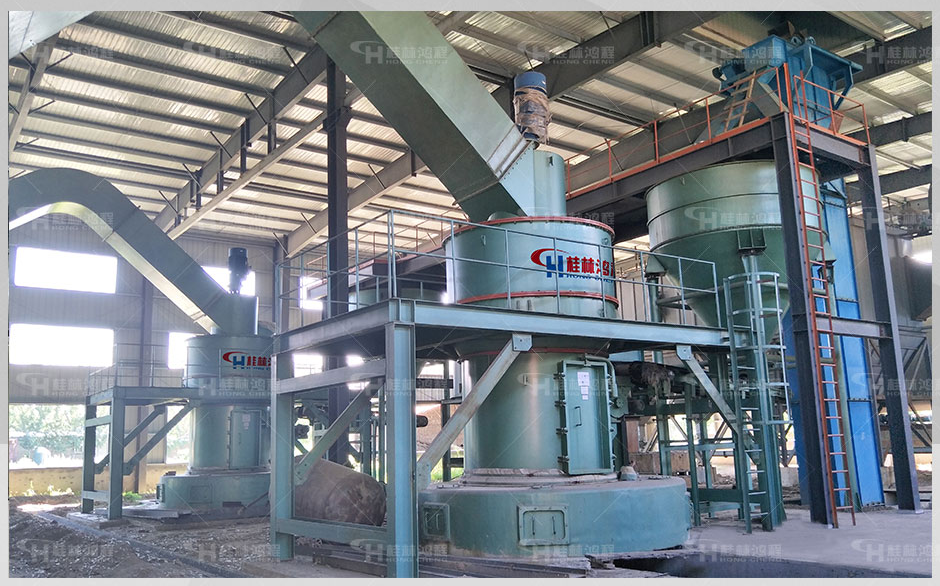
01、Advantages and Characteristics
1. The bowl coal mill has strong adaptability and can process various types of coal, including cheap and low-quality coal, as well as high ash and high moisture coal;
2. Low operating vibration, no need to use spring damping foundation, equipped with a main motor with lower power than other medium speed coal mills, energy-saving and consumption reducing;
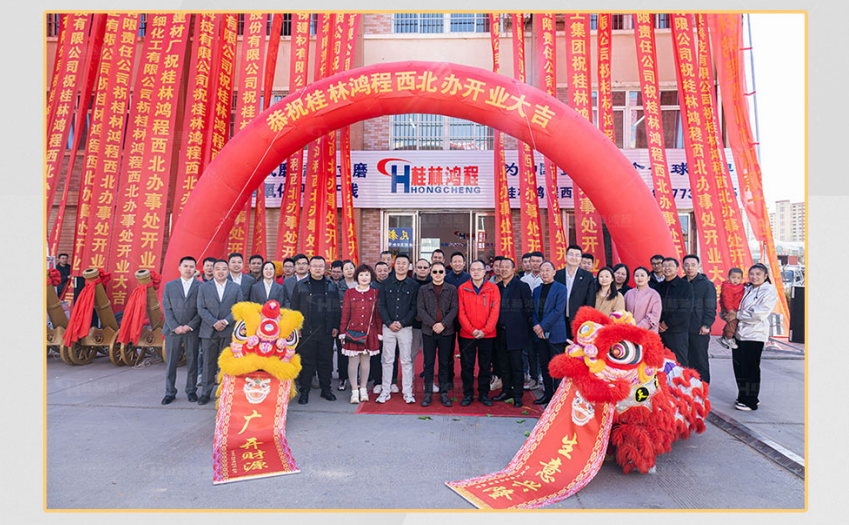
3. The grinding roller has no direct contact with the grinding bowl liner, can be started without load, has a wide load adjustment range, and is allowed to operate at 25-100% load;
4. The structure is simple and reasonable, with no dead corners for powder accumulation. The maximum resistance of a single wind is less than 4.5Kpa (in plain areas), and the separator can withstand an explosive pressure of 0.35Mpa;
5. The grinding roller can be directly flipped out for maintenance and replacement. Each grinding bowl liner plate weighs about 25kg and can be manually moved. The grinding roller loading device is located outside the separator body, making maintenance convenient;
6. The grinding roller sleeve is made of wear-resistant alloy welding, which has a long service life and can be repeatedly welded 5-6 times after wear, reducing operating costs;
7. Adopting a PLC fully automatic control system, which can achieve remote control, easy operation, convenient maintenance, and reduce labor costs;
8. Small in size, low in height, and lightweight, its concrete foundation only requires 2.5 times the weight of the entire machine, resulting in low overall investment costs.
02. Selection of Guilin Hongcheng Coal Powder Production Line
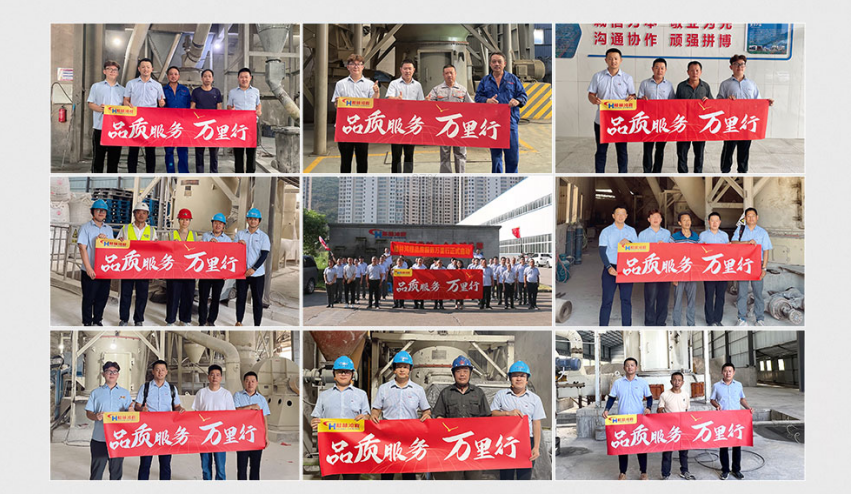
Post time: Sep-18-2024