vertical grinding mill is an industrial equipment widely used in cement, mining, chemical and other industries. It is mainly used to grind various raw materials such as ores and stones into fine powder. The design structure of the vertical grinding mill is compact and the operation is efficient. It can complete the grinding and classification of materials in one go. So, how does the vertical grinding mill work? As a professional vertical grinding mill manufacturer, Guilin Hongcheng will introduce you to the operating procedures and details of the vertical grinding mill today.
1. How does a vertical grinding mill work?
Simply put, the working process of a vertical grinding mill is like the process of pressing a large stone into powder, except that the "stone" here is various mineral raw materials, and the "pressing" force comes from the grinding roller. The material enters the rotating grinding disc through the feeding device. As the grinding disc rotates, the material is thrown to the edge of the grinding disc under the action of centrifugal force. In this process, the grinding roller is like a huge rolling pin, using strong pressure to crush the material into fine powder. The fine powder will be carried to the upper part of the mill by the high-speed airflow , and after being screened by the "powder selector", the fine powder becomes the finished product, and the coarse particles are returned to the grinding disc for further grinding.
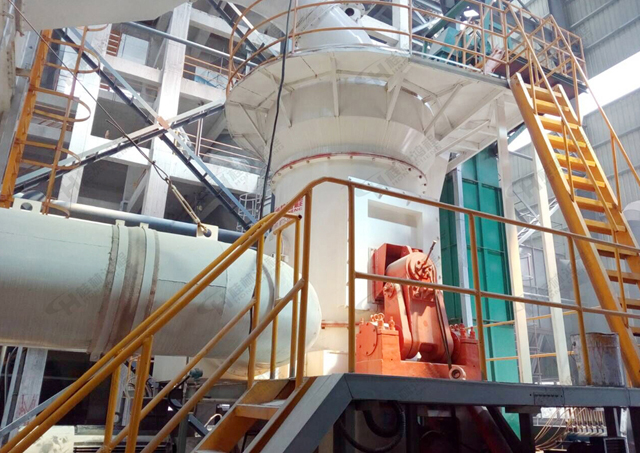
2. vertical grinding mill Operating Procedures
• Wear labor protection equipment.
• Two people are required to inspect and repair the vertical grinding mill together and keep in touch with the central control at all times. A dedicated person must be left outside the mill to provide safety monitoring.
• Before entering the vertical grinding mill, low-voltage lighting must be used.
• Before entering the vertical grinding mill, cut off the power supply of the vertical grinding mill main motor, exhaust fan feeding equipment, and powder selection machine, and turn the on-site control box to the "maintenance" position.
• When replacing the grinding roller lining and parts, pay attention to prevent collision and injury, and take safety precautions.
• When working at height, the operator should first ensure that the tools are intact and in good condition, and fasten the safety belt.
• When you have to enter the mill for inspection during the operation of the kiln, you must take safety precautions, keep in close contact with the central control, arrange special personnel to be responsible for safety work, and increase the high-temperature fan exhaust at the kiln tail. The hot air baffle at the mill inlet must be closed and powered off, and the system negative pressure must be stable;
• After confirming that the grinding body has been fully cooled, find out the dust accumulation depth and temperature of the mill. If the mill is overheated, not exhausted, or has too much dust, it is strictly forbidden to enter. At the same time, you must pay attention to whether there is material accumulation on the feeding chute to prevent it from slipping and injuring people.
• Complete the power outage procedures in accordance with relevant regulations.
3. What are the core components of vertical grinding mill?
• Transmission device: The "power source" that drives the grinding disc to rotate, which is composed of a motor and a reducer. It not only drives the grinding disc to rotate, but also bears the weight of the material and the grinding roller.
• Grinding device: The grinding disc and grinding roller are the key to the vertical grinding mill. The grinding disc rotates, and the grinding roller crushes the material like a pair of rolling pins. The design of the grinding disc and grinding roller can ensure that the material is evenly distributed on the grinding disc, ensuring efficient grinding.
• Hydraulic system: This is the key part to control the roller pressure. The pressure applied by the roller to the material can be adjusted according to the different hardness of the material to ensure the grinding effect. At the same time, the hydraulic system can also automatically adjust the pressure to protect the mill from damage when encountering hard objects.
• Powder selector: Like a "sieve", it is responsible for screening out the ground materials. The fine particles become finished products, and the larger particles are returned to the grinding disc for re-grinding.
• Lubrication device: The mill needs to be lubricated frequently to run smoothly. The lubrication device can ensure the normal operation of all important parts of the equipment and avoid downtime or damage due to wear.
• Water spray device: Sometimes the material is too dry, which can easily affect the grinding effect. The water spray device can increase the humidity of the material when necessary, help stabilize the material layer on the grinding disc, and prevent the mill from vibrating.
4. Advantages of vertical grinding mill
Compared with traditional ball mills, vertical grinding mills have lower energy consumption, higher efficiency, and smaller footprint, making them suitable for large-scale industrial production. In addition, vertical grinding mills can be flexibly adjusted according to different material types and grinding requirements, making them more convenient to operate. In general, vertical grinding mills are advanced grinding equipment that processes various ore raw materials into fine powder through the cooperation of grinding rollers and grinding discs, and play an important role in many industrial fields. For more grinding mill information or quotation request please contact with us.
Post time: Dec-30-2024